
TECHNOLOGY | LSAW Linepipe
We use the JCO and four roll bending processes to produce longitudinal submerged arc welded (LSAW) pipe for our linepipe products.
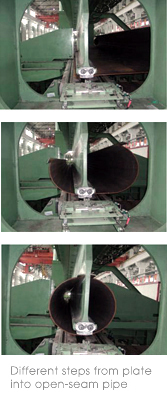
JCO Process
The JCO forming process, which uses a forming press as the primary forming aggregate, has become more common in recent years compared with the UOE process and the four roll bending process due its greater flexibility, higher quality product and lower investment costs.
In addition to the production of thick-walled and large diameter pipes, the JCO forming process is excellent for producing small diameter pipe with large wall thickness, making it ideal for the production of offshore linepipe.
In the JCO process the plate – milled and crimped at the edges – is delivered to a forming press, shifted into position for bending by manipulators, and formed into an open seam pipe, using a die matched to the pipe dimension, across the entire plate length in stages. First, one side of the plate is bent to form a half-round – the “J “ in “JCO”. The plate is then shifted by a second manipulator to bring the opposite side into position to be bent in the same way, forming the “C“and then the completing the “O“. The open-seam pipe thus formed is sufficiently rounded, with plane-parallel edges, to be ready for welding.
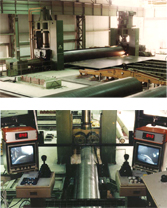
Roll Bending
In the roll bending process the plate is formed into an open seam pipe by several passes through a 4 roll bending machine. The open edges are not formed, instead remaining straight. Once formed, the open seam pipe is transported to an edge bending machine where the two longitudinal edges of the plate are crimped by rolls in a continuous process